
Robotic Arm Truss
May 2019 to Aug 2019
-
Designed the mechanical, electrical and control system of pick and place robotic arm using SolidWorks, proteus and MATLAB.
-
Utilized mathematical models and simulations to replicate the electromechanical system behavior before building the system.
-
Integrated Arduino Uno as a microcontroller with the system and programmed feedback control using MATLAB .

Mechanical
Three design were made using SolidWorks and final design was chosen by doing comparison between the designs using FEA analysis and decision matrix.

Design 1

Design 2

Design 3
Decision Matrix
The decision matrix helped us come up with the best design. The matrix table depicts that design - 3 is the recommended one as it has the highest weighted score.

Electrical
An electronic circuitry is necessary since the signals from the computer cannot provide enough power to drive the motor and the electromagnet.
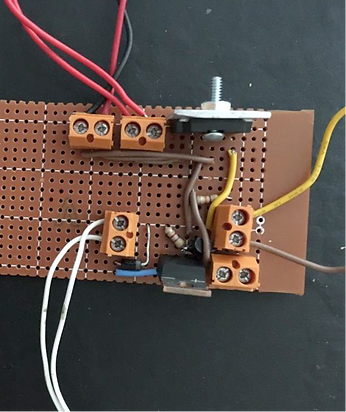
Front of the Protoboard with H-Bridge driver and circuit for the Electromagnet Control
Heat Sink Design
Electronic components generate considerable amount of heat during normal operation. Most common method to control excessive heat dissipation in electronic components is heat sink.
To avoid any damages to IC, heat sink was design using formulas and data sheets of the components used in circuit design.

Heat sink for H-Bridge motor driver
Heatsink for electromagnet
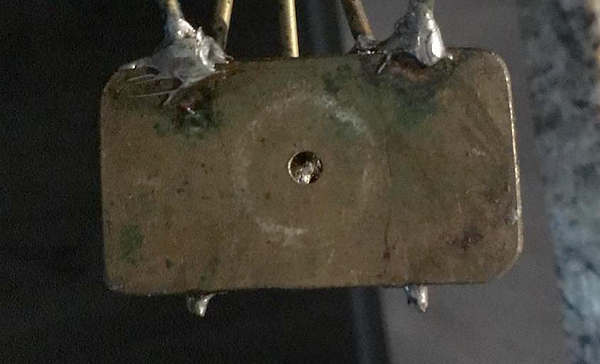
Experimental result using MATLAB before building final prototype
DC Motor
DC motor is connected to the function generator via Toshiba H-Bridge Motor Driver and 12V power supply. The PWM signal with 5V amplitude and 2.5V offset is applied with different duty cycles to control the speed of the motor. The input and ground wires are switched to control the direction of the motor.

DC Motor Experimental Plot of Terminal Voltage against Duty Cycle (CW)
DC Motor Experimental Plot of Terminal Voltage against Duty Cycle (CCW)

Electromagnet
A linear inverse relationship of terminal voltage and duty cycle can be seen from the simulation. The simulated result in the MATLAB Simulink and measured values are approximately similar.
Theoretical

The average DC voltage at the output (electromagnet) is approximately 0V when 99% of the duty cycle is applied and the average output DC motor is approximately 12V when 1% of the duty cycle is applied.
Experimental

Average terminal voltage across the electromagnet is recorded using digital multimeter with different duty cycles.
Control System
The whole system was modelled using MATLAB simulink to have a better insight into the process i.e determining the stability and the proper constant values.
The transfer function of the system were created for speed and position of the motor control: with and without load on the motor. We have used MATLAB’s built-in function and also a Custom Code for PID controller.
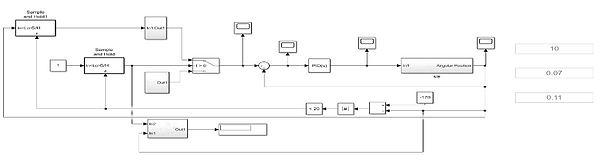
The complete Simulink model that controlled the system was created keeping in mind all necessary aspects of the project like moment of inertia of the truss arm, the capabilities of the motor being used, the max power ratings of the electrical components.
Angular Displacement
.png)
As we can see above the we had the initial offset of 30 degrees and the signal went form the 30° to -150° (a difference of 180°). Then we see a sudden rise, this is because now it had reached the 180° and so the initial point for the second signal is now set to whatever the real position is. Then we see some dead time this is so because we want our bridge to wait at that point for a while to fulfil the criteria. Then we slowly rise to the -90° from the new Setpoint.
Input Signal
As we can see from the real time response is also quite close to the input signal. There is a part were the signal seems noisy, this is because the encoder is itself not very accurate when it comes to small changes in angular position.

Output Real Response
Angular Velocity
The output angular velocity of the motor is quite fast and it follows almost similar to the input signal given to it. It can be seen the signal is quite noisy this is due to systematic error in our optical motor encoder.
Input Signal

Output Real Response

The whole project tested our overall skills in mechanical, electrical and software department. The entire integrated system functioned correctly, as each part of the design (electrical, mechanical and controller) were integrated effectively to meet the overall requirements of the project.